在食品加工行业,设备的稳定运行对于保障产品质量、生产效率以及企业的经济效益至关重要。随着工业物联网技术的飞速发展,设备远程运维成为了食品加工企业提升竞争力、优化生产管理的关键手段。通过远程运维,企业能够实时监控设备状态、预测故障、及时响应并进行远程维护,从而减少设备停机时间、降低运维成本,并确保生产过程的连续性和可靠性。
食品加工企业设备远程运维的基础架构与技术实现
(一)设备连接与数据采集
1、传感器部署
在食品加工设备上部署各类传感器,如温度传感器、压力传感器、湿度传感器、振动传感器等。以烘焙设备为例,温度传感器可精确监测烤箱内的温度,确保烘焙过程符合工艺要求。这些传感器能够采集设备运行过程中的关键参数,并将其转换为电信号或数字信号。
对于液体处理设备,如饮料灌装机,流量传感器可实时监测液体的流量,压力传感器监控管道内的压力,以保证灌装的准确性和稳定性。
2、数据传输方式
采用有线与无线相结合的传输方式。在工厂内部,对于一些固定位置且对数据传输稳定性要求极高的设备,如大型食品加工生产线的核心设备,可利用有线以太网连接,确保高速、稳定的数据传输。
对于一些移动设备或分布较为分散的辅助设备,如仓库中的叉车、小型包装设备等,则采用无线传输技术,如 Wi-Fi、4G或工业专用的低功耗广域网技术。这些无线技术能够在保证一定数据传输速率的同时,降低设备连接成本和功耗。
3、数据采集频率
根据设备的运行特性和数据的重要性确定采集频率。例如,对于制冷设备,其温度数据可能需要每几分钟采集一次,以确保温度始终处于食品保鲜所需的合适范围。而对于一些高速运转且故障风险较高的设备,如食品切片机的振动数据,可能需要每秒采集多次,以便及时捕捉异常振动信号,预防设备故障。
(二)数据处理与存储
1、边缘计算
在靠近设备端设置边缘计算节点,如TDE工业网关。这些边缘计算设备能够对采集到的原始数据进行初步处理,例如过滤掉噪声数据、进行数据压缩以及简单的数据分析,如计算设备的实时运行效率、能耗指标等。以食品加工中的研磨设备为例,工业网关可根据振动传感器数据实时判断研磨轮的磨损情况,并将初步分析结果与原始数据一起上传到云端。
工业网关还能够在网络中断等情况下,暂时存储数据,并在网络恢复后自动将数据上传,确保数据的完整性。
2、云端存储与管理
经过工业网关处理后的数据被上传到云端服务器。云端采用分布式存储架构,对海量的设备数据进行存储。
数据在云端按照设备类型、工厂区域、时间序列等多维度进行分类管理,以便于后续的数据查询、分析和挖掘。例如,食品加工企业可以方便地查询某一特定生产线在过去一个月内的设备运行数据,分析设备性能的变化趋势。
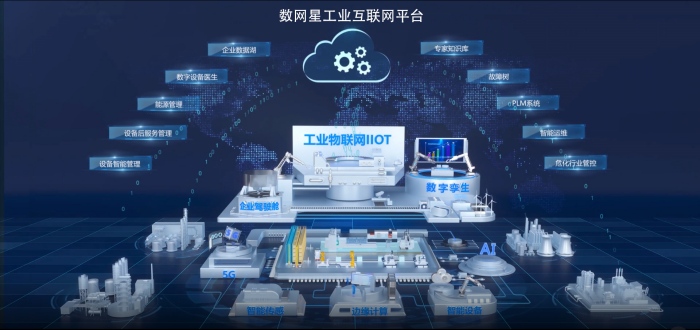
(三)远程监控与可视化
1、监控平台搭建
依托数网星平台基座开发的设备远程监控平台,该平台基于 Web 技术或移动应用程序(APP),使企业管理人员、运维工程师等能够随时随地访问设备运行数据。监控平台采用直观的图形化界面,如仪表盘、趋势图、报警列表等,展示设备的关键参数、运行状态和历史数据。
以乳制品加工企业为例,监控平台可实时显示牛奶杀菌设备的温度、压力曲线,以及设备的启停状态、故障报警信息等。运维人员通过手机 APP 就能快速了解设备情况,即使不在工厂现场也能及时做出响应。
2、报警与预警机制
在监控平台中设置智能报警与预警系统。根据设备的正常运行范围和历史数据,设定阈值。当设备参数超出阈值时,系统自动触发报警,并通过多种方式通知相关人员,如短信、邮件、APP 推送等。
例如,对于油炸食品加工设备,如果油温过高超过设定的安全阈值,系统立即发出报警,提醒运维人员采取降温措施,防止火灾隐患或食品质量问题。同时,预警系统还能够基于数据分析预测设备可能出现的故障,如根据某食品包装机的电机电流波动趋势,提前预警电机可能存在的故障风险,以便企业提前安排维护计划,避免突发故障导致的生产中断。
食品加工企业的设备远程运维是工业物联网技术在食品行业的重要应用领域。通过构建完善的基础架构、实现核心功能、应对各种挑战,食品加工企业能够实现设备的智能化管理,提升生产效率、降低成本、保障食品质量安全,从而在激烈的市场竞争中取得优势。