一、企业生产困境
该汽车制造企业拥有庞大且复杂的生产线,涵盖冲压、焊接、涂装、总装等多个环节,各类设备来自不同供应商,通信协议五花八门,如PLC之间的Profibus-DP、机器人控制系统的Ethernet/IP以及传感器的Modbus RTU等。这就导致设备之间的数据难以共享,形成 “信息孤岛”,生产管理部门难以及时、精准掌握设备运行状态,故障排查耗时费力,严重制约生产效率提升,并且质量管控也因数据滞后而存在漏洞,无法满足日益严苛的市场需求。
二、工业通信网关选型与部署
为打破僵局,企业经严谨评估,选用TDE具备多协议转换功能、高可靠性工业通信网关。在部署环节,依据生产线布局,于关键节点——各车间中控室及设备集中区域安装网关。以冲压车间为例,将网关与多台冲压机PLC连接,通过网关内置的协议转换模块,把Profibus-DP协议数据转换为统一的OPC UA协议,以便上传至车间级MES系统;在焊接车间,针对弧焊机器人与周边辅助设备,网关实现Ethernet/IP到MQTT的转换,确保机器人焊接参数、焊点质量数据实时传输至云平台供工艺工程师分析优化。
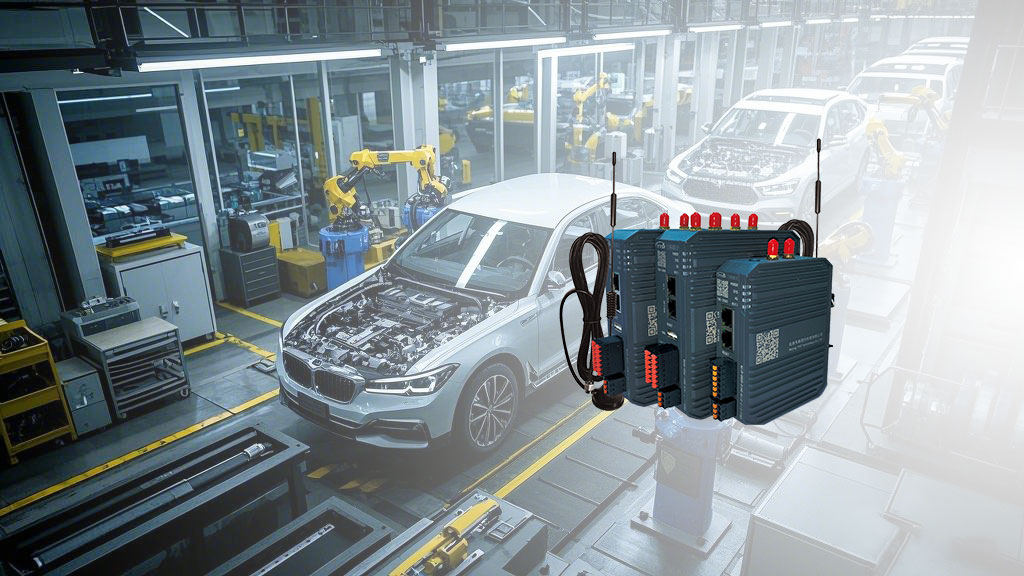
三、带来的显著效益
(一)实时生产监控与调度优化
部署通信网关后,企业管理层通过可视化大屏,可实时查看各车间设备开机率、产量、故障报警等信息。如总装车间,一旦某条装配线出现设备故障停机,网关瞬间将故障信息推送至调度中心,维修人员能依据详细故障代码与位置迅速响应,平均故障修复时间从原来的2小时缩短至40分钟,生产线综合效率(OEE)提升15%,生产排期更精准,有效避免订单延误。
(二)质量精准管控
涂装车间借助网关采集喷枪压力、漆料流量、烘干温度等工艺参数,实时比对预设质量标准范围。一旦参数异常波动,立即触发预警并反馈至工人终端与质检系统,次品率从3%降低至1.5%,同时通过对历史数据深度挖掘,优化涂装工艺参数,提升漆面均匀度与光泽度,产品外观质量显著提高,市场售后反馈故障率降低20%。
(三)预测性维护落地
通过长期收集设备运行数据,如电机电流、振动频率、轴承温度等,利用网关上传至大数据分析平台,建立设备健康模型。以冲压机为例,系统提前一周预测到关键零部件磨损风险,安排预防性更换,避免突发停机造成的高额损失,设备维护成本整体降低10%,设备使用寿命延长8%,为企业稳定生产筑牢根基。