一、引言
在自动化生产线中,电机扮演着至关重要的角色,它们为各种设备的运转提供动力,直接影响着生产的效率、质量以及整体稳定性。而对电机的数据采集,则能够让我们实时掌握电机的工作状态,实现预防性维护、优化控制策略以及保障整个生产线的顺畅运行,具有十分重要的意义。
二、电机数据采集的重要参数
1、电流数据
电流是反映电机负载情况的关键指标。当电机正常运行时,其工作电流会在一个相对稳定的范围内波动,与电机的额定功率以及所驱动负载的大小相关。例如,如果电机驱动的设备突然遇到卡顿等过载情况,电流会瞬间增大,超出正常范围。通过实时采集电流数据,我们可以及时发现电机是否存在过载、堵转等异常,避免电机因长时间过载而损坏。
2、电压数据
电压的稳定与否对电机的正常运行影响重大。电机需要在合适的额定电压下工作,电压过高可能会导致电机绝缘被击穿,而过低则可能使电机无法输出足够的转矩,无法正常带动负载运转。持续采集电压数据,可以监测电网供电质量,判断是否存在电压波动、欠压或过压等问题,以便及时采取稳压等相应措施。
3、转速数据
转速体现了电机的运行速度,对于很多自动化生产工序,要求电机按照特定的转速来驱动设备,以保证生产节拍和产品加工精度等。比如在流水线上的输送带电机,必须保持稳定的转速才能确保产品匀速传输。通过传感器采集转速数据,能够确认电机是否按照设定的转速运行,并且还可以据此分析电机的调速性能以及传动系统是否存在打滑等故障。
4、温度数据
电机在运行过程中会产生热量,尤其是长时间高负载运转时,其内部绕组等部件温度会升高。正常情况下,电机有一定的散热机制来维持温度在安全范围内,但如果散热不良或者负载异常增大,温度就可能过高,从而影响电机的绝缘性能,降低使用寿命,甚至引发故障。所以实时监测电机的温度数据,能提前预警过热风险,采取降温等措施保障电机可靠运行。
5、振动数据
电机运行时的振动情况反映了其机械结构的健康状态。例如,电机的轴承磨损、转子不平衡、安装基础松动等问题都会导致振动加剧。采集振动数据,并分析振动的幅值、频率等特征,可以精准判断电机是否存在机械故障隐患,有助于安排合适的维护时间,避免故障扩大化,影响整个生产线的正常生产。
三、常用的数据采集方法和传感器
1、电流传感器
常用的有霍尔电流传感器,它基于霍尔效应工作。当有电流通过导线时,会在其周围产生磁场,霍尔元件置于该磁场中,会产生与磁场强度相关的霍尔电势,经过后续电路的处理,就能输出与被测电流成比例的电信号,从而实现对电机电流的精确测量。这种传感器具有精度高、响应速度快、线性度好等优点,能适应不同电流大小范围的电机测量需求。
2、电压传感器
电压互感器是一种常见的电压测量传感器,它通过电磁感应原理,将高电压按比例变换为低电压信号,方便后续采集设备进行测量和处理。对于低压电机,也可以采用分压电阻等简单电路构成的电压采集模块,将电机的供电电压按合适比例衰减后采集相应的电压值,为监测电机的电压状况提供数据支持。
3、转速传感器
光电式转速传感器应用较为广泛。它一般由发光元件和光电接收元件组成,在电机的旋转轴上安装有带孔或反射条纹的圆盘,随着电机转动,光线会周期性地被遮挡或反射,光电接收元件接收到的光信号就会产生相应的脉冲变化,通过对脉冲频率的计数和计算,就能得出电机的转速。另外,还有电磁感应式转速传感器等,利用电磁感应原理,根据电机旋转部件产生的磁场变化来测量转速,不同类型的转速传感器适用于不同的应用场景。
4、温度传感器
对于电机温度测量,常用的有热电阻温度传感器和热电偶温度传感器。热电阻温度传感器是利用金属材料的电阻随温度变化的特性,通过测量其电阻值来换算出对应的温度值,其测量精度较高,在电机的绕组、外壳等部位安装后,可以准确反映电机关键部位的温度情况。热电偶温度传感器则是基于热电效应,由两种不同的金属材料组成闭合回路,当两端存在温度差时会产生热电势,通过测量热电势来确定温度,它能够适应较宽的温度范围,在电机高温区域测量时有独特优势。
5、振动传感器
加速度传感器是测量电机振动的常用传感器类型。它能够感受电机振动产生的加速度变化,并将其转换为电信号输出。通过对加速度信号进行积分等处理,可以进一步得到振动的速度和位移信息,从而全面分析电机的振动特征。通常将加速度传感器安装在电机的外壳等关键部位,以便准确捕捉电机运行时的振动情况。

四、数据采集系统的架构
1、传感器层
由上述各类传感器组成,它们分布在电机的不同关键部位,如在电机的进线端安装电流、电压传感器,在电机轴附近安装转速传感器,在外壳安装温度和振动传感器等,负责实时采集电机相应的运行参数,并将这些物理量转化为电信号输出。
2、信号调理层
由于传感器输出的信号往往比较微弱,可能还存在噪声干扰等情况,信号调理层的作用就是对这些信号进行放大、滤波、线性化等处理,使其变成符合后续采集设备要求的标准信号,提高数据的准确性和可靠性。例如,通过滤波电路去除信号中的高频杂波,通过放大电路将微弱信号放大到合适的幅值范围。
3、数据采集设备层
这一层通常采用数据采集卡或者专门的工业数据采集网关(如TDE网关),它们接收经过信号调理后的信号,将模拟信号转换为数字信号,并按照一定的采样频率对数据进行采集和量化,然后将这些数字化的数据传输到上层的监控系统中。数据采集设备需要根据实际的采集需求选择合适的采样频率、分辨率等参数,以确保能准确获取电机运行状态的关键信息。
4、监控与分析系统层
在这一层,通过相应的软件平台(如数网星云平台)对采集到的数据进行实时显示、存储以及深入分析。操作人员可以直观地看到电机各项参数的实时数值、变化曲线等,当参数超出设定的正常范围时,系统会发出报警提示。同时,借助数据分析算法,如基于机器学习的故障诊断算法等,可以对电机的健康状态进行评估,预测潜在故障,为制定维护计划提供有力依据。
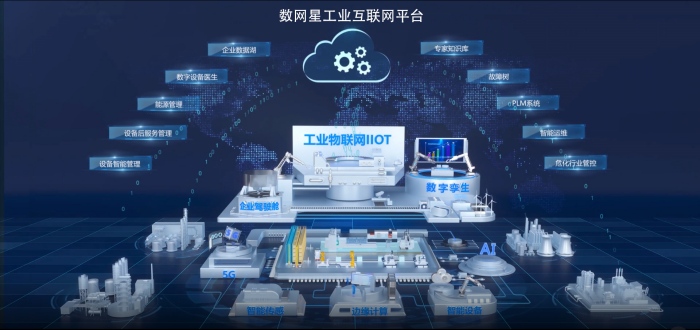
五、数据采集的应用与优势
1、故障诊断与预防性维护
通过长期持续采集电机的数据,并分析数据的变化趋势和异常情况,可以提前发现电机可能存在的故障隐患,如通过电流的异常波动判断电机内部绕组是否有短路趋势,根据振动幅值的增大判断轴承磨损情况等。这样就能在故障还未真正发生、对生产造成严重影响之前,安排针对性的维护工作,更换磨损部件等,有效降低设备的维修成本,提高设备的整体可用性。
2、优化控制策略
根据采集到的电机转速、电流等数据,可以了解电机在不同负载情况下的实际运行性能,进而优化对电机的控制策略。例如,在自动化生产线的调速系统中,依据电机实时转速反馈,精确调整变频器的输出频率,使电机更精准地按照生产工艺要求的转速运行,提高生产的精度和质量,同时也有助于节能降耗,提高能源利用效率。
3、生产过程监控与管理
电机作为自动化生产线的动力核心,其运行状态直接关系到整个生产过程的稳定性。实时采集电机数据并集成到整个生产线的监控系统中,管理者可以全面了解生产线各环节电机的工作情况,及时发现因电机问题导致的生产中断风险,便于统筹安排生产计划,保障生产的高效、有序进行。
六、结语
在自动化生产线中,电机的数据采集是实现智能化生产、保障设备可靠运行的关键环节。通过准确采集电机的各项关键参数,利用合适的采集方法和系统架构,并充分发挥采集数据在故障诊断、控制优化以及生产管理等方面的作用,能够显著提升自动化生产线的整体性能和效益,推动制造业向更高水平的自动化、智能化方向发展。