一、CNC网关的核心功能
(一)多协议转换
CNC机床作为工业生产中的精密加工设备,通常采用各种特定的工业通信协议,如Profibus-DP、Modbus、CANopen等。然而,企业上层管理系统如ERP、MES往往基于以太网TCP/IP协议运行。CNC网关能够无缝对接这些异构协议,将机床端采集的数据转换成通用网络协议,确保数据顺畅地在车间与办公室之间流通,打破信息孤岛,实现全流程数据共享。
(二)设备数据采集
精准、实时的数据采集是智能生产的基石。CNC网关具备强大的数据采集能力,可从机床控制器、驱动器、传感器等多个数据源获取丰富信息。涵盖机床的运行状态,如开机、关机、待机、加工;加工参数,包括切削速度、进给量、刀具补偿;以及设备健康指标,像电机温度、主轴振动、润滑油压等。通过对这些数据的高频采集,为后续分析决策提供了详尽素材,助力企业实时掌控生产一线动态。
(三)远程监控与诊断
借助工业物联网技术,CNC网关让远程监控机床运行成为现实。无论身处工厂车间的任何角落,还是远在千里之外的办公室,工程师和管理人员都能通过PC、平板或智能手机等终端,直观地查看机床实时画面、关键数据指标及历史趋势曲线。一旦设备出现故障预警,专业人员还可利用网关的远程诊断功能,在线调取机床报错信息、运行日志,如同亲临现场般迅速排查问题根源,大大缩短停机时间,降低维修成本。
(四)边缘计算
为应对海量实时数据传输带来的网络带宽压力与云端处理延迟难题,CNC网关集成了边缘计算功能。在数据源头附近,它能依据预设规则对采集的数据进行初步分析、筛选、聚合。例如,实时判断加工过程是否超出公差范围,统计设备在一段时间内的开机利用率等。仅将有价值的关键数据上传至云端或上层系统,既减轻网络负担,又加速决策响应,确保生产的连续性与高效性。
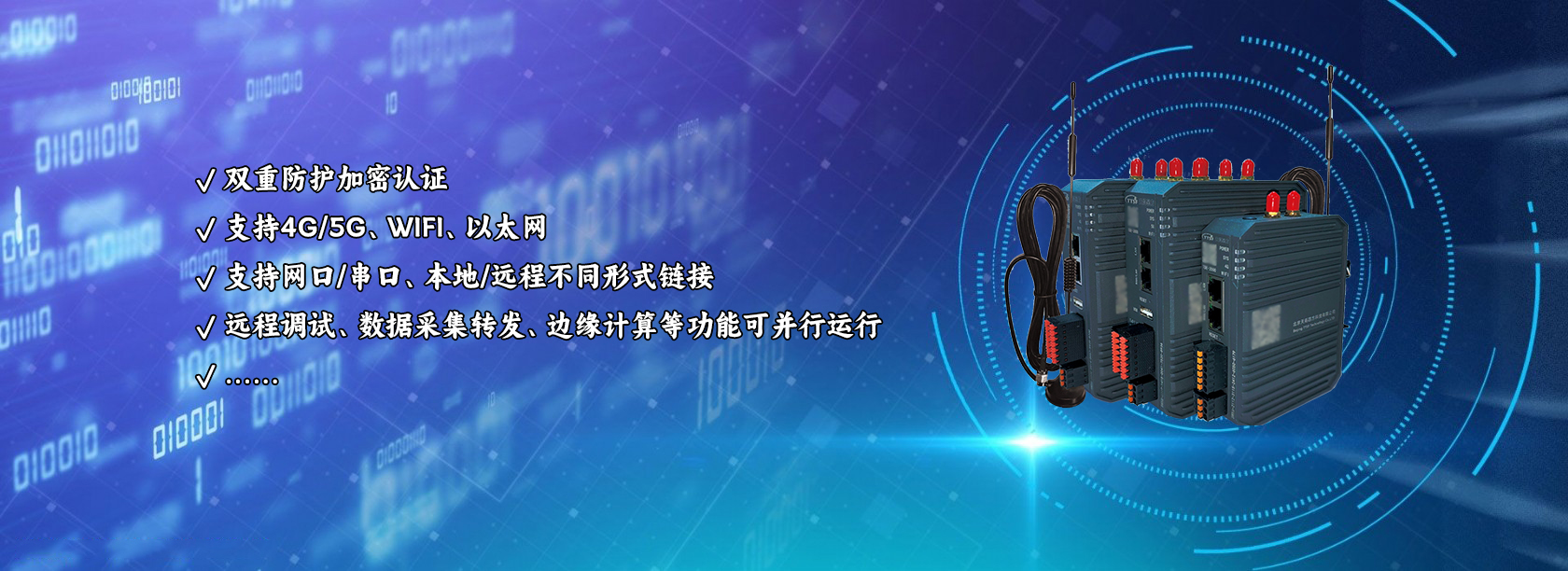
二、CNC网关的典型应用场景
(一)智能工厂建设
在智能工厂架构中,CNC网关是实现车间数字化、智能化的关键基础设施。通过将多台CNC机床接入统一的物联网平台,企业可构建起透明化生产车间。实时数据反馈至MES系统,助力生产排程动态优化,根据设备实际负荷合理分配工单;质量管控部门依据加工参数实时监测,及时捕捉次品风险,提升产品整体合格率;设备维护团队基于设备健康数据,从传统的事后维修向预防性维护转变,精准安排保养计划,延长设备使用寿命,全方位提升工厂运营效益。
(二)分布式制造协同
随着制造业全球化分工趋势加剧,跨地区、跨企业的分布式制造模式愈发普遍。CNC网关使得不同地域工厂的CNC设备能够互联互通。总部企业可远程监控各地分厂的生产进度、质量状况,统一调配技术资源、工艺标准;供应链上下游企业间,通过共享关键设备数据,实现紧密协同,如零部件供应商依据整机厂CNC加工需求,精准调整生产节奏、优化库存管理,确保整个产业链的高效顺畅运作。
(三)柔性定制生产
面对日益个性化的市场需求,柔性生产成为制造业竞争力的核心要素。CNC网关配合先进的数控系统,能够快速响应订单变化。在生产过程中,根据实时采集的订单信息、产品设计参数,动态调整机床加工工艺,实现不同批次、不同规格产品的快速切换生产。同时,将生产过程中的实际数据反馈至设计研发端,为产品迭代优化提供依据,以柔性制造能力满足客户多样化定制诉求,抢占市场先机。