一、钢铁生产工厂场景
钢铁生产涉及多个复杂且相互关联的工艺流程,包括炼铁、炼钢、轧钢等环节。在各个环节中,存在海量的设备参与运行,例如炼铁环节的高炉,其内部有温度、压力、流量等多种传感器用于监测炉内状况;炼钢时的转炉需要实时反馈转速、倾动角度等参数;轧钢线上的轧机更是要精确传递轧制力、轧制速度以及设备的振动情况等数据。同时,还有众多的自动化控制系统、电机设备等,共同保障钢铁生产的顺利进行。
二、物联网采集网关应用需求分析
1.多设备兼容与连接需求
钢铁生产线上设备类型繁多,不同年代、不同厂家的设备并存,通信协议和接口五花八门。比如老式的温度传感器可能采用模拟量输出,通过4-20mA电流信号传输,而新的自动化控制系统大多基于以太网通信,采用如OPC UA等协议。这就需要物联网采集网关能够兼容多种接口(如RS232、RS485、以太网等),并支持大量不同的协议,实现对各类设备的统一连接。
2.恶劣环境适应性需求
钢铁生产环境恶劣,高温、粉尘、强电磁干扰等情况普遍存在。在炼铁高炉附近,温度常常高达上百度,且存在大量的铁屑粉尘;炼钢区域也有很强的电磁干扰。因此,物联网采集网关要能在这样的极端环境下稳定可靠地工作,确保数据采集不间断。
3.实时数据采集与传输需求
钢铁生产过程是连续且不容许长时间中断的,像高炉的温度、压力等参数一旦出现异常,必须及时反馈,以便操作人员快速做出调整,避免安全事故以及保证产品质量。所以采集网关要能实时采集各设备数据,并迅速传输到监控系统进行分析处理。
三、物联网采集网关的具体应用
(一)网关选型与特点
以天拓四方的工业物联网采集网关为例,其具有以下适合该场景的特点:
1.丰富的接口与协议支持:配备多个RS485、RS232串口以及以太网接口,可连接各种基于串口通信或以太网通信的设备。在协议方面,广泛支持Modbus(RTU/TCP)、OPC UA等常见工业协议以及众多设备自定义协议,通过简单配置就能实现对钢铁厂内不同设备的数据采集。
2.工业级防护设计:具备高防护等级的外壳,能够有效防尘、防水、抗冲击,内部电路采用特殊的电磁屏蔽和散热设计,可在-40℃至85℃的宽温环境下正常工作,很好地适应了钢铁厂高温、多尘、强电磁干扰的恶劣环境。
3.数据处理与传输能力:内置高性能处理器,在采集数据后能进行一定的数据预处理,如滤波、数据格式转换等,减少数据传输量及后续监控系统的处理压力。支持多种传输方式,如通过有线以太网或无线(如4G/5G)方式将数据实时传输到本地服务器或远程的云平台。
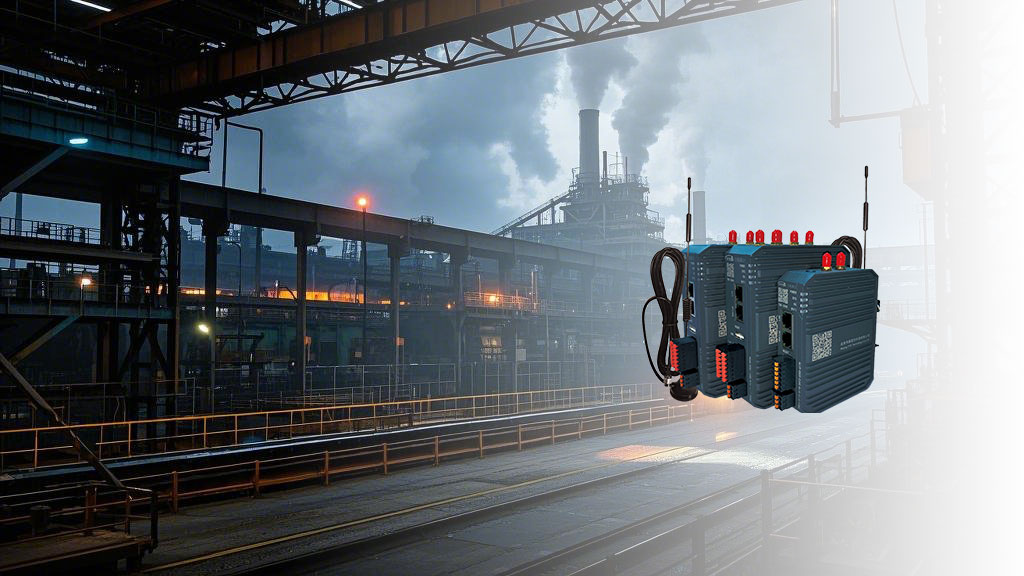
(二)具体应用方式
1.设备接入与配置
在炼铁环节,对于高炉上的温度传感器(采用4-20mA模拟量输出),通过信号调理模块将模拟信号转换为数字信号后接入网关的RS485接口,在网关配置软件中选择对应的模拟量采集模块,并设置好量程范围(如0-1000℃对应的电流值范围)等参数,使其准确采集温度数据。对于高炉的压力传感器(若采用Modbus RTU协议),直接将其RS485通信线连接到网关的RS485接口,在网关中配置好Modbus RTU协议的相关参数,如站地址、波特率、数据位、停止位等,实现压力数据的采集。
在轧钢环节,轧机的控制系统往往基于以太网通信且采用OPC UA协议,将网关通过以太网接口连接到轧机控制系统所在的网络,在网关中配置OPC UA客户端相关参数,指定要采集的数据节点(如轧制力、轧制速度等参数对应的节点地址),完成轧机数据的接入。
2.数据预处理与传输
网关采集到高炉的温度、压力数据以及轧机的运行参数后,会进行数据的预处理。例如,对温度数据进行滤波处理,去除因电磁干扰等原因产生的异常波动值,然后按照一定的时间间隔(如每5秒)将经过整理的数据通过有线以太网方式传输到钢铁厂的本地监控系统服务器。
对于部分关键数据,如高炉炉内压力出现急剧变化等紧急情况,网关可立即触发报警机制,通过短信、邮件等方式通知相关运维人员,并同时将实时数据优先传输到监控系统,以便及时采取应对措施。
3.监控与决策支持应用
本地监控系统服务器接收到网关传来的数据后,进行可视化展示,在监控大屏上以图表、曲线等形式实时呈现高炉各参数变化情况、轧机的运行状态等,方便生产调度人员、技术人员直观地掌握生产状况。
通过大数据分析技术,结合历史数据和当前实时数据,对钢铁生产过程进行质量分析、故障预测等操作。例如,根据高炉历史温度、压力数据以及当前的变化趋势,提前预测可能出现的炉况异常情况,为操作人员调整配料、风量等参数提供决策依据,保障钢铁生产的稳定和产品质量。
四、应用效果与优势
1.提高生产安全性:通过实时监测关键设备和工艺参数,能够及时发现如高炉超压、轧机过载等安全隐患,提前预警并采取措施,有效减少安全事故的发生概率,保障人员和设备安全。
2.提升产品质量:精确掌握生产过程中的各项参数,便于及时调整工艺参数,优化生产流程,使得钢铁产品的质量更加稳定,成材率得到显著提高,例如从原来的约90%提升到95%左右。
3.降低运维成本:实现远程监控和故障预测后,运维人员可以提前准备维修工具和配件,有针对性地进行设备维护,减少了设备突发故障导致的停机时间,降低了维修成本和设备更换成本,同时也减少了现场巡检的人力成本。
总之,在钢铁生产这样复杂且恶劣的工业场景下,物联网采集网关凭借其强大的设备连接、数据采集与处理、传输以及适应环境等能力,为钢铁企业的智能化生产、安全保障以及高效运营发挥了关键作用,并且这种应用模式可在类似的重工业生产场景中广泛推广和落地实施。