一、案例背景
某大型制造企业拥有多条自动化生产线,每条生产线上配备了众多不同型号的PLC设备,用于控制各类生产环节,如电机运转、物料输送、加工工序的自动化执行等。然而,随着企业规模的扩大以及对生产管理精细化要求的提升,传统的本地查看PLC数据、人工记录的方式已经难以满足需求。企业迫切需要一种能够实时采集PLC数据,并可实现远程监控、数据分析的解决方案,以此来提高生产效率、快速定位故障以及优化生产流程。
二、解决方案选择——PLC数据采集网关
经过多番调研与评估,企业最终选择引入天拓四方PLC数据采集网关来解决上述问题。该网关具备以下关键特性与功能:
协议兼容性强:能够兼容市面上主流的PLC通信协议,像西门子的S7协议、三菱的MC协议、欧姆龙的FINS协议等。这确保了可以无缝连接生产线上不同品牌、不同型号的PLC设备,避免了因协议不兼容而产生的数据采集障碍。
数据采集精准高效:可以按照预设的时间间隔(如每隔1秒)或者特定的触发条件(例如某个设备状态改变时),准确地从PLC寄存器、数据位等存储区域采集各类生产数据,包括设备运行状态参数(如电机转速、温度、压力等)、生产节拍数据、故障报警信息等。
远程通信能力:支持多种网络通信方式,例如以太网、4G/5G无线通信等,能够将采集到的数据实时传输到企业的远程监控中心服务器,无论监控人员身处何地,只要有网络连接权限,都可以通过上位机软件或者网页端界面访问这些数据。
三、实施过程
1、网关安装与配置
在每条生产线上的合适位置安装PLC数据采集网关,通过通信线缆(如网线、RS485线等根据具体PLC接口和协议要求)将网关与各个PLC设备进行连接。技术人员依据PLC的具体型号、IP地址(如果是以太网连接方式)以及通信协议等参数,对网关进行详细的配置,确保其能准确识别并建立与每台PLC的通信链路,设定好要采集的数据点和采集频率等关键信息。
2、网络搭建与调试
针对企业的网络环境,选择通过企业内部的以太网为主干网络,同时为部分较偏远或者不方便布线的生产线配置了4G无线通信模块作为备用网络链路,确保数据传输的稳定性和持续性。在网络搭建完成后,进行了严格的网络连通性测试和数据传输调试,对出现的丢包、延迟等问题及时排查并解决,保障采集到的数据可以准确无误地发送到远程监控中心。
3、远程监控平台搭建
在企业的监控中心服务器上部署了数网星云平台,该平台与PLC数据采集网关进行对接,能够接收、解析和展示网关传来的各类PLC数据。通过可视化界面,以图表(如实时折线图展示设备温度变化趋势)、仪表盘(直观呈现设备关键性能指标的数值和状态)、列表(罗列故障报警信息等)等多种形式呈现数据,方便监控人员查看和分析。
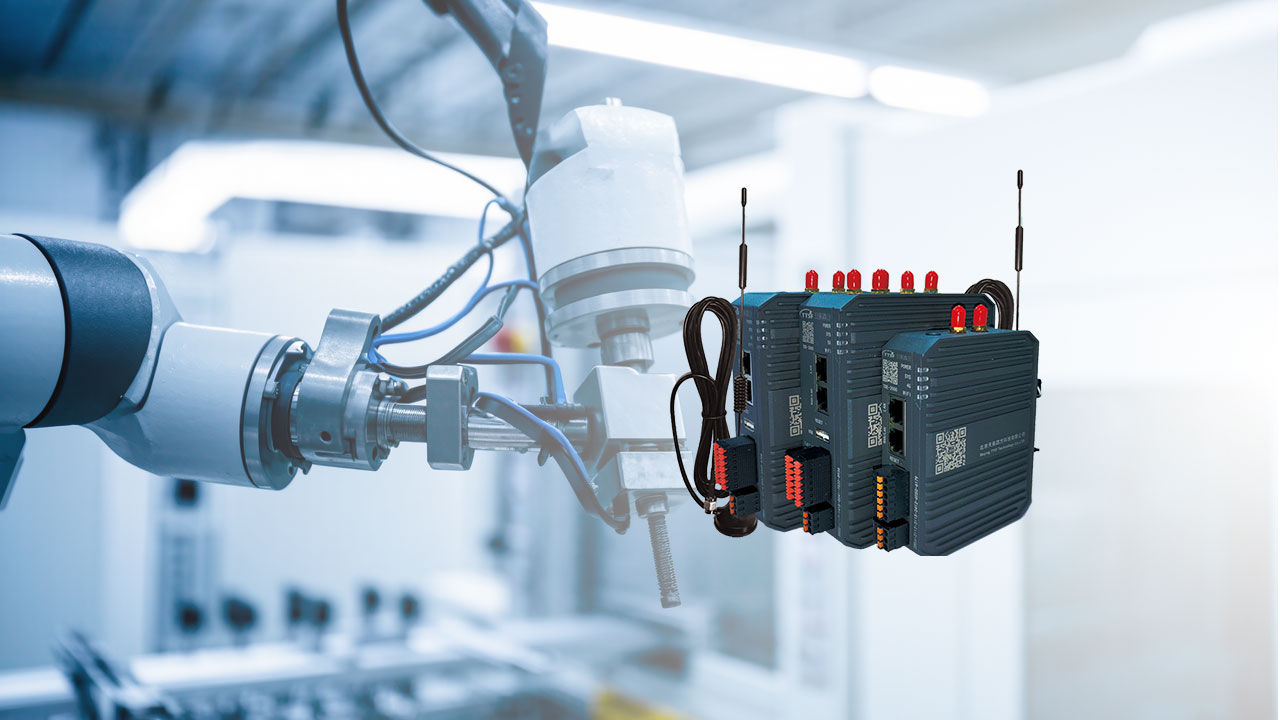
四、应用效果分析
1、生产效率提升
通过实时采集PLC数据,监控人员可以清晰地掌握每条生产线的实际运行情况,及时发现生产环节中的瓶颈所在。例如,通过分析物料输送环节中各输送设备的运行数据,发现某段输送带的速度设置不合理,导致物料堆积、影响后续加工工序的衔接,经过调整后,生产线整体节拍更加流畅,单位时间内的产品产出量提升了约15%。
2、故障快速定位与处理
以往设备出现故障时,需要维修人员到现场逐个排查PLC程序和设备硬件情况,耗时较长。现在一旦有设备故障报警信息通过网关传送到远程监控平台,维修人员可以远程查看相关设备的详细运行数据,迅速判断是PLC控制逻辑问题、传感器故障还是其他机械部件的问题。例如,之前某电机频繁出现过载停机故障,借助采集到的电机实时电流、转速等数据以及历史趋势分析,维修人员很快确定是电机所带负载的传动部件出现卡滞,及时更换部件后恢复了正常生产,故障排查时间从原来的平均2小时缩短到了30分钟以内。
3、数据驱动的生产优化
积累的大量PLC数据经过进一步的数据分析(如利用大数据分析工具进行相关性分析、趋势预测等),为企业的生产工艺优化提供了有力支撑。比如,通过分析不同加工参数下产品的质量数据(通过连接检测设备的PLC获取质量检测结果)以及对应的生产设备运行参数,找到了最佳的加工参数组合,产品的合格率从原来的90%提升到了95%,同时降低了原材料的浪费。